Inside the Box: The Modular Way to Build a Cleanroom
By Dawn Patton Mangine
The traditional image of a cleanroom is a conventionally built room inside a regular building with stark white walls and people in white sterile gowns completing their production work. However, a modular cleanroom is a break from the past, providing a faster timeline for completion and allowing operations to gain time and profit to start process and production lines sooner.
When Pharmaceutical Product Development (PPD, Inc.), part of Thermo Fisher Scientific, needed a cleanroom, they initially contacted a traditional general contractor for a proposal. PPD operates the largest GMP (good manufacturing practices) testing lab in Middleton, Wisconsin, testing pharmaceuticals.
According to Jessica Phillips, senior group leader for PPD, “We were designing quickly and with flexibility in mind because we’re onboarding many new technologies.” Discussions with the general contractor (GC) were stalled, and Phillips decided to call on the Fisher Scientific team for input on the matter.
“It was good to have other opinions on calls to talk through everything because [we were] trying to get to market as soon as possible,” Phillips said.
Cleanroom in a Box
While the GC was pushing for a traditional build—what’s known in the industry as a “stick” build—Deborah Haring, Fisher Scientific controlled environments and production specialist, had a different idea. She advised that a more appropriate solution was a modular, prefabricated controlled environment.
Because customers in biotech and pharmaceuticals can experience a growth phase and have shortened timelines as a result, “We like to recommend a prefabricated cleanroom,” said Kristine Tiangco, Fisher Scientific regional safety specialist for Illinois and Wisconsin. This gives the customer the flexibility to configure the environment to their needs on an expedited timeline, which in this instance was faster than the traditional stick-build timeline proposal by over two months.
With the modular cleanroom, which Tiangco called a “cleanroom in a box,” a lab can configure an empty space to become an ISO-5 aseptic cleanroom or an ISO-8 non-classified space. The interconnecting panels are composed of high-quality, non-shedding, non-conductive materials that can withstand the rotations of cleaning, disinfection, sanitation, and sporicidal chemicals. The materials lend themselves to a long lifespan of the modular space.
If the space needs to be reconfigured, it’s simply a matter of reconfiguring walls. Haring explained that with a modular lab, it’s easy for the client to expand or contract their footprint and even pick up and relocate the modular cleanroom down the road to a new location and building when desired.
Phillips confirmed that both speed and flexibility were two urgent factors for PPD. “We needed that flexibility, so when we found how a test would run, we could make those changes as we go.”
Another reason to choose a modular build, said Haring, is sustainability. “We help the customer check the box on sustainability because when you choose modular over the existing methods, there’s no carbon footprint of building materials on a work site.” The manufacturing detritus does not impact the customer. All the components are constructed offsite and shipped to the worksite to erect. “It’s a very nice, green presentation.”
Expertise and Trust
The modular cleanroom at PPD is set up in a 2,000-square-foot building. It contains biosafety cabinets, where most of the testing is done. The lab is non-classified with the biosafety cabinets rated to ISO level 5.
Phillips explained that the cabinets are used for mycoplasma testing. “Mycoplasma is very small, less than two microns (>0.2 microns), and it can easily infect cell lines.” The modular setup with the cabinets mitigates contamination risk, which was a big concern, Phillips said. Having a separate lab for mycoplasma allowed PPD to prioritize their workflows and pass-throughs for this testing.
In addition to the cleanroom, the Fisher Scientific channel supplied the biosafety cabinets, stainless steel benches, and guidance for operating procedures, such as gowning protocols and cleaning tools and solutions.
"We are able to build it, make it sustainable, make it operational.” Deborah Haring, Controlled Environments and Production Specialist
“We are able to build it, make it sustainable, make it operational, and give them a much better result at the end of the day with their whole process,” Haring said. “They hit the easy button when they called us.”
Tiangco said, “We hit the big three for PPD: a faster timeline, appropriate materials, and lower costs.” She added, “What I’m most proud of is the strong, exhaustive, consultative relationship we were able to build with our customers.”
For more information on cleanrooms and other types of research facility construction that the Fisher Scientific channel can provide, visit fishersci.com/new-facility-support.
Dawn Patton Mangine is a Thermo Fisher Scientific staff writer.
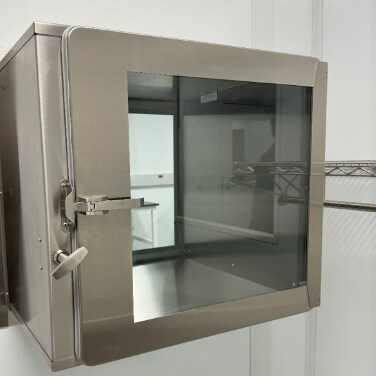
Photo of a cleanroom pass-through by Rose Tichava, Laboratory Builders, Inc.